How Defoamers Enhance Efficiency in Manufacturing and Production
How Defoamers Enhance Efficiency in Manufacturing and Production
Blog Article
The Function of Defoamers in Enhancing Product Top Quality and Performance
Defoamers offer as important ingredients that mitigate this issue, guaranteeing smoother production process while boosting the functional and visual characteristics of the last products. The option of the ideal defoamer can be critical to attaining optimal outcomes, elevating vital concerns about formula compatibility and efficiency metrics that warrant more expedition.
Understanding Defoamers
Comprehending the duty of defoamers is vital for maintaining product quality across numerous sectors. Defoamers are chemical additives designed to protect against the development and reduce of foam in fluid systems, which can negatively affect processes such as blending, filling up, and surface area stress. Lathering can lead to ineffectiveness, product defects, and compromised visual appeal, making defoamers an important component in making procedures.
In industrial applications, defoamers assist to enhance product consistency and security. The efficient usage of defoamers not just makes sure smoother manufacturing processes yet likewise adds to exceptional item performance.
Moreover, the option and formula of a defoamer have to line up with details application demands, such as compatibility with other active ingredients, effectiveness under differing temperature and pH problems, and prospective regulative restrictions. Ultimately, comprehending defoamers' functions and their value in numerous solutions is vital for optimizing production and guaranteeing the finest quality end items.
Kinds of Defoamers
Defoamers can be categorized into several kinds based on their composition and system of action. The key types consist of silicone-based, non-silicone natural, and not natural defoamers.
Silicone-based defoamers are among one of the most effective, mostly as a result of their ability to spread promptly on the fluid surface area and disrupt foam formation. Their unique chemical structure enables superior security, making them appropriate for high-temperature applications and atmospheres with varying pH levels.
Non-silicone organic defoamers, commonly composed of natural oils or fats, are valued for their biodegradability and reduced toxicity. These are usually used in food and beverage applications where security and ecological influence are vital.
Inorganic defoamers, which consist of materials like talc or calcium carbonate, act by raising the thickness of the fluid, therefore decreasing foam stability. They are frequently utilized in industrial processes where compatibility with various other products is not a problem.
Each kind of defoamer has distinct advantages and limitations, permitting tailored options relying on the certain frothing problems experienced in numerous applications. Recognizing these distinctions is critical for optimizing efficiency and accomplishing desired item top quality.
Applications Throughout Industries
Many markets utilize defoamers to boost product high quality and functional efficiency. In the food and drink field, defoamers are critical in procedures such as brewing and dairy manufacturing to stop foam formation, which can bring about inefficiencies and item variance. By controlling foam, producers can guarantee far better return and a much more consistent item.
In the pharmaceutical sector, defoamers play a vital duty in the formulation of liquid medications, where excessive foam can hinder blending and accurate dosing. Their use helps maintain the stability of the solutions and assists in smoother manufacturing processes.
The paint and coverings market also depends on defoamers to enhance the performance of products throughout application. By reducing foam, these additives ensure a smoother coating and enhance the aesthetic qualities of the final product.
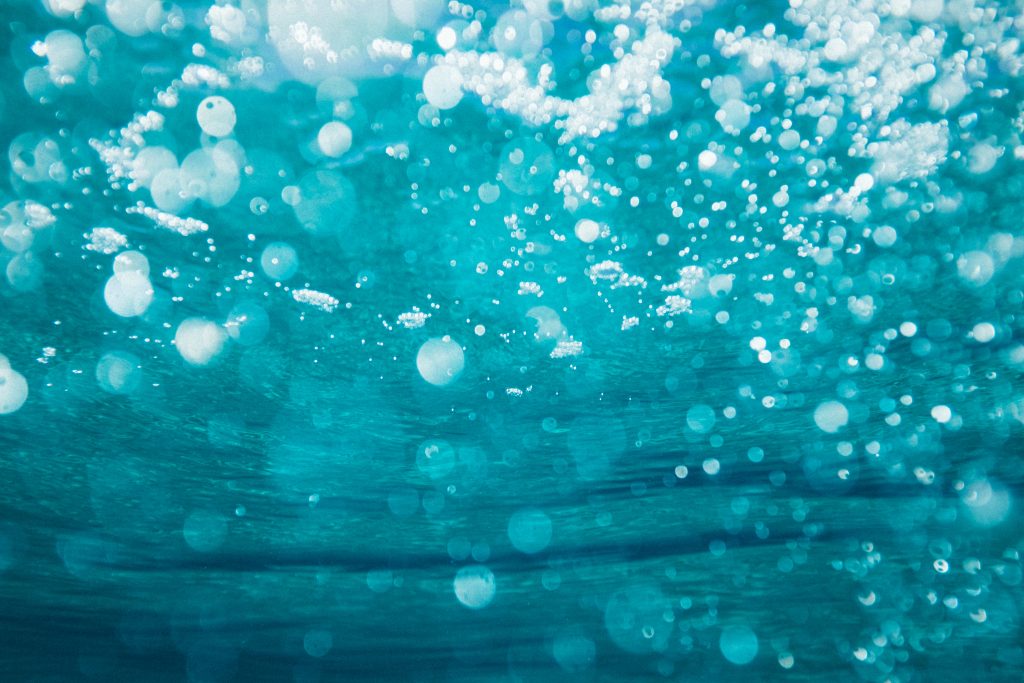
Advantages of Utilizing Defoamers
While the application of defoamers varies across markets, their benefits constantly improve item quality and procedure efficiency. One considerable benefit is the decrease of foam development during making processes, which can or else cause production hold-ups and disparities in product quality. By reducing foam, defoamers make it possible for a smoother site link flow of products, facilitating more efficient operations and minimizing the possibility of tools malfunctions.
Furthermore, making use of defoamers can improve the appearance and texture of end products. In industries such as layers, paints, and food processing, extreme foam can compromise the visual aesthetic appeals and general top quality, while the suitable defoamer application ensures a consistent surface and preferable attributes. Defoamers can contribute to cost financial savings by decreasing waste during production and optimizing the use of raw products.

Selecting the Right Defoamer
Picking the appropriate defoamer is crucial for enhancing manufacturing procedures and making certain product high quality. The selection of defoamer affects not just the effectiveness of foam control yet additionally the overall performance qualities of the end product. Elements to consider include the type of application, the chemistry of the solution, and the ecological conditions under which the item will certainly be made use of.
Different sectors may require specific defoamer kinds, such as silicone-based, natural, or polymeric defoamers. Understanding the compatibility of the defoamer with the main components is important to prevent adverse reactions that can jeopardize product honesty. Furthermore, the defoamer's performance in numerous temperature levels and pH degrees need to be reviewed to ensure consistent performance.
Testing the defoamer in small check this applications can give beneficial insights right into its efficiency and suitability. Factor to consider of regulative conformity, specifically in food, drugs, and cosmetics, is critical in picking a defoamer. Ultimately, a detailed evaluation of these aspects will lead to the option of a defoamer that not just controls foam properly but likewise enhances the top quality and efficiency of the end product.
Verdict
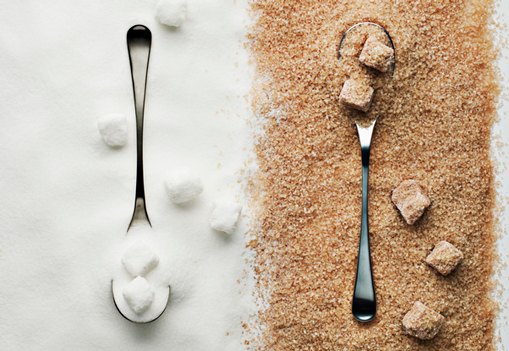
In conclusion, defoamers are crucial additives that dramatically improve product high quality and efficiency across different markets. The tactical option and application of defoamers lead to cost financial savings, enhanced resource usage, and increased consumer contentment.
Lathering can lead to ineffectiveness, product defects, and jeopardized visual appeal, making defoamers an important component in producing operations.
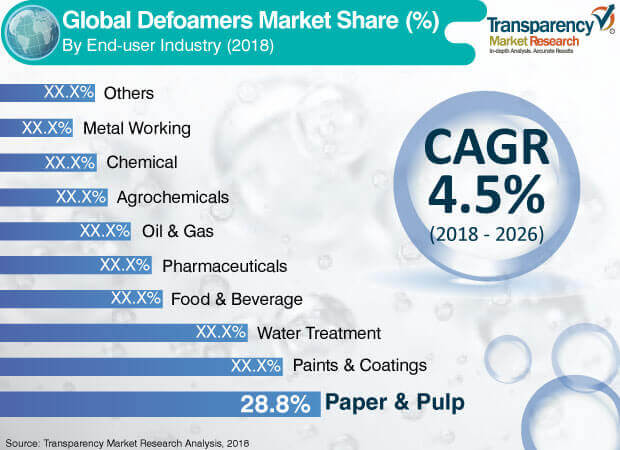
Report this page